Liquid Cooling in Data CenterData centers power our digital lives, from streaming services to cloud apps and e-commerce platforms. However, the exponential rise of AI, big data analytics, and edge computing has pushed traditional cooling methods to their limits.
Conventional air-cooling systems struggle to dissipate heat effectively at high densities, leading to thermal throttling, downtime risks, and inflated energy costs. Meanwhile, environmental mandates and corporate sustainability goals demand lower carbon footprints and reduced water usage.
Liquid Cooling in Data Centers is emerging as the definitive strategy for thermal management. By circulating coolant directly to heat sources—via cold plates, immersion baths, or rear-door exchangers—liquid systems deliver unparalleled efficiency, performance, and eco-friendliness.
Benefits and Rationale Behind Liquid Cooling
Liquid Cooling in Data Centers transcends mere hype; it addresses core challenges in modern infrastructure.
Escalating Compute Demands Demand Better Cooling
As organizations deploy AI clusters, GPU-accelerated servers, and edge nodes, heat densities have surged. A single high-end GPU can dissipate up to 500 watts of heat, and dense racks can exceed 50 kW per rack. Air cooling struggles with these loads, requiring more fans, larger chillers, and higher airflow rates, which consume significant power and increase noise. In contrast, liquid cooling handles concentrated heat fluxes directly at the chip level, maintaining stable temperatures under peak loads. For data centers aiming for 5G, AI inference, or blockchain mining, liquid cooling is no longer optional—it’s essential.
Unmatched Thermal Management and Operational Efficiency
Coolants like engineered glycol blends and dielectric fluids boast thermal conductivities far superior to air. They remove heat up to ten times faster, reducing hotspots and offering precise temperature control. This leads to:
- Stable Performance: Consistent thermal conditions prevent thermal throttling during peak workloads.
- Energy Savings: Studies show up to 60% reduction in cooling-related energy consumption.
- Extended Hardware Lifespan: Lower temperature variance reduces thermal stress, extending component life by up to 30%.
- Compact Footprint: Higher rack densities without bulky air handling systems.
Discover how Reboot Monkey’s Liquid Cooling in Data Centers solutions can reduce your PUE below 1.2—book a free assessment today.
Environmental and Energy Efficiency Benefits
Liquid cooling aligns with sustainability commitments by cutting both energy and water usage.
Dramatic Energy Savings and Carbon Reduction
A typical air-cooled data center spends 30–40% of its total power on cooling. Liquid cooling can slash that to under 10%. For a 2 MW facility, this translates to savings of 10–15 GWh annually—enough to offset the energy consumption of over 1,500 homes. Carbon emissions drop proportionally, helping organizations meet Scope 2 reduction targets and achieve carbon-neutral certifications.
Case Study: Global Financial Institution
This firm retrofitted 200 GPU racks with cold plate liquid cooling. The outcome:
- PUE dropped from 1.85 to 1.25.
- Annual energy costs fell by $4.2 million.
- CO₂ emissions reduced by 2,300 metric tons per year.
Water Conservation and Sustainability Impact
Water scarcity concerns are rising globally. Traditional evaporative cooling towers withdraw millions of liters annually, impacting local ecosystems. Closed-loop liquid systems avoid evaporation, recycling coolant indefinitely. Data center operators report zero water loss in immersion setups, conserving vital resources and avoiding regulatory risks in water-stressed regions.
Example: Hyperscaler Z’s Immersion Plant
Located in an arid zone, Hyperscaler Z’s facility uses a two-phase immersion loop with dielectric fluid. Benefits:
- 100% sealed system with no water evaporation.
- Zero water discharge into local watershed.
- Alignment with corporate net-zero water goals.
Learn how Reboot Monkey’s water-saving liquid cooling designs can support your sustainability roadmap.
Performance Advantages for Modern Infrastructure
Liquid cooling doesn’t just save energy; it unlocks new performance capabilities for cutting-edge workloads.
Enhanced CPU and GPU Efficiency
Direct-to-chip cooling offers minimal thermal resistance, keeping processors close to coolant inlet temperatures (often 25–30°C). This stability:
- Enables Overclocking: Servers can run at higher clock speeds safely.
- Maintains Throughput: No dynamic frequency scaling or throttle events during VR/AR simulation, financial modeling, or AI training.
- Improves Reliability: Consistent temperatures reduce memory errors and component degradation.
Edge and Hyperscale Use Cases
Edge Deployments: Portable liquid-cooled modules maintain telecom base stations in harsh climates. They require minimal space and can handle ambient temperatures up to 55°C.
Hyperscale Racks: Immersion-cooled racks push densities to 400+ kW, enabling next-gen AI clusters and supercomputing nodes without expanding data hall footprints.
Types and Technologies of Liquid Cooling
Different architectures cater to varied requirements—here’s a closer look at each.
Direct-to-Chip (Cold Plate) Cooling
Cold plates feature microchannel designs that maximize surface contact with CPUs and GPUs. Parallel flow channels ensure even distribution, while quick-connect fittings simplify maintenance. Key considerations:
- Material Selection: Copper vs. aluminum cold plates trade off thermal conductivity vs. weight.
- Loop Layout: Series vs. parallel loops impact flow rates and pressure drop.
- Compatibility: Custom cold plates exist for major CPU/GPU form factors.
Leading Providers: Asetek, CoolIT, Vertiv.
Liquid Immersion Cooling
Full Immersion: Servers sit in dielectric tanks; heat transfer occurs through fluid convection.
Partial Immersion: Only high-wattage components are immersed, reducing fluid volume.
- Single-Phase Systems: Liquid remains below boiling point; external heat exchangers remove heat.
- Two-Phase Systems: Fluid boils at hot spots; vapor rises and condenses, offering higher heat flux removal.
Innovators: Submer, Iceotope, GRC, Asperitas.
Rear-Door Heat Exchangers and Hybrid Models
Rear-door exchangers replace standard rack doors with liquid-cooled plates. Exhaust air passes through the door, transferring heat to coolant. Combined with under-floor air systems, hybrid setups offer balanced performance and retrofit ease.
- Retrofit Speed: Install in hours without server disassembly.
- Performance Trade-Off: Best for moderate densities (up to 20 kW/rack).
Vendors: Rittal, Fujitsu, Rittal’s LCP series.
Top Hard Drive Shredding Companies in Amsterdam: Easy & Certified Data Destruction | Reboot Monkey
Market Trends and Competitive Landscape
Stay ahead by understanding financial, strategic, and technological shifts in the liquid cooling arena.
Data Center Liquid Cooling Market Growth
- 2024 Market Value: $1.2B.
- 2027 Projection: $2.5B (CAGR ~25%).
- Key Drivers: AI/ML scale-out, HPC modernization, ESG mandates.
Major Players and Innovators
- Publicly Traded: Asetek (ASETEK.US), Vertiv (VRT.US), Eaton (ETN.US).
- Private Disruptors: Submer, Iceotope, GRC, Asperitas.
- M&A Activity: Major HVAC firms acquiring liquid cooling startups to broaden portfolios.
Tracking Liquid Cooling Data Center Stocks
Investor interest is high: ASETEK.US and VRT.US have risen 18% year-to-date, outperforming NASDAQ Composite by 10%. Analysts cite long-term contracts with hyperscalers and cloud providers as growth catalysts.
Implementation Considerations
Avoid pitfalls by following a structured deployment roadmap.
Implementing Liquid Cooling: A Step-by-Step Guide
- Site Audit: Evaluate power distribution, floor loading, and existing cooling infrastructure.
- Thermal Analysis: Use CFD modeling to map hotspots and design loop architectures.
- Technology Selection: Choose cold plate, immersion, or hybrid based on density, budget, and water constraints.
- Engineering Design: Draft P&IDs, specify pumps, manifolds, heat exchangers, and reservoir sizing.
- Deployment: Conduct dry runs, leak tests, and integrate with BMS for monitoring.
- Commissioning & Training: Validate performance metrics, train staff on maintenance and emergency procedures.
Key Design and Operational Best Practices
- Redundancy Planning: Implement N+1 or 2N for pumps and heat exchangers.
- Coolant Chemistry: Select fluids with low viscosity, high dielectric strength, and biocide additives.
- Monitoring & Automation: Integrate flow meters, temperature sensors, and leak detectors into centralized dashboards.
- Maintenance Protocols: Schedule periodic fluid sampling, filter replacements, and sensor calibrations.
Challenges and Barriers
Identify and mitigate common concerns.
Leak Risks and Mitigation Strategies
Fears around fluid leaks deter some operators. However, advancements in high-density quick-connect fittings, real-time leak detection sensors, and automatic shutdown protocols have dramatically improved safety. Best practices include redundant seals, drip trays, and routine pressure testing.
Managing CAPEX vs. OPEX
Liquid cooling systems cost 15–30% more initially. Yet, energy and maintenance savings typically yield ROI within 2–4 years. Financial modeling should incorporate:
- Energy Price Projections: Higher electricity costs accelerate payback.
- Maintenance Savings: Fewer mechanical fans and smaller chillers reduce service contracts.
- Incentives: Government grants for energy-efficient upgrades can offset CAPEX.
China built hundreds of AI Data Centers To Catch The AI Boom | Reboot Monkey
Vendor Lock-In and Ecosystem Interoperability
Proprietary loop architectures risk future lock-in. Selecting open-architecture manifolds, standardized fittings (e.g., G1/4″) and industry-supported protocols helps preserve flexibility. Engage multiple vendors for best-of-breed solutions.
Future Outlook and Innovations
Stay at the forefront by monitoring emerging trends.
Next-Gen Cooling for AI and Quantum Computing
Generative AI clusters and quantum testbeds demand extreme cooling—sub-20°C fluid loops and cryogenic immersion. Research prototypes using liquid nitrogen and supercritical fluids aim to meet qubit cooling requirements and next-level AI density.
Integration with Renewable Energy and Smart Grids
Smart data centers will synchronize liquid cooling loops with dynamic renewable energy availability. Real-time controls adjust pump speeds and heat exchanger setpoints based on solar output or wind generation, maximizing green energy usage and minimizing grid impact.
Modular, Portable, and Edge-Centric Innovations
Plug-and-play liquid-cooled modules will power disaster recovery sites, pop-up HPC clusters, and 6G edge nodes. Standardized 20-foot containers with pre-installed liquid loops allow rapid deployment and easy relocation.
Comparative Analysis: Liquid vs. Traditional Cooling
A head-to-head comparison reveals why liquid cooling outperforms air and phase-change systems in modern data centers.
Thermal Performance
- Air Cooling: Relies on ambient air; struggles beyond 300 W of heat per rack unit, leading to hotspots.
- Phase-Change Cooling: Uses refrigerants to absorb heat through evaporation; efficient but complex, requiring compressors and leak-tight systems.
- Liquid Cooling: Direct-to-chip and immersion offer heat removal rates exceeding 1,000 W per chip, maintaining uniform temperatures across high densities.
Energy and Water Efficiency
- Air: High fan power and chiller loads; significant water use in evaporative towers.
- Phase-Change: Moderate energy footprint; minimal water use but higher mechanical complexity.
- Liquid: Up to 60% lower cooling energy; closed loops eliminate water evaporation.
Deployment Complexity
- Air: Easiest retrofit but limited future scalability.
- Phase-Change: Complex piping and maintenance; limited vendor options.
- Liquid: Moderate complexity; modern quick-connects and modular designs simplify installation.
What You Need To Know About Smart Hands Services | Reboot Monkey
Safety, Standards, and Regulations
Ensuring compliance and operational safety is crucial for liquid-cooled facilities.
Industry Standards
- ASHRAE TC 9.10: Provides guidelines for liquid cooling safety and thermal performance.
- ISO/IEC 30134: Defines metrics for energy efficiency (PUE) and water usage effectiveness.
Leak Detection and Prevention
- Sensors: Pressure, flow, and moisture sensors trigger alarms and automatic shutdown.
- Containment: Drip trays, secondary piping, and encapsulated fittings minimize damage risks.
Regulatory Compliance
- Environmental Permits: Closed-loop systems often avoid wastewater regulations due to zero discharge.
- Electrical Codes: Liquid systems must meet NEC standards for conduit penetration and equipment grounding.
Total Cost of Ownership and Financial Modeling
A detailed TCO analysis helps justify liquid cooling investments and forecast ROI.
Capital Expenditure (CAPEX)
- Equipment Costs: Cold plates, pumps, heat exchangers, and manifold assemblies.
- Installation: Site preparation, piping, and commissioning labor.
Operational Expenditure (OPEX)
- Energy Savings: Reduced fan and chiller power; direct correlation to electricity price fluctuations.
- Maintenance: Longer refresh cycles for chillers, simplified air filter logistics, and fluid top-offs.
Payback Periods and Incentives
- ROI Timelines: Typical payback in 2–4 years based on 0.10–0.15 USD/kWh electricity rates.
- Incentives: Tax credits, utility rebates, and green financing programs accelerate ROI.
Skills, Training, and Organizational Change
Adopting liquid cooling entails new operational roles and training priorities.
Workforce Development
- Fluid Handling Expertise: Training technicians on coolant chemistry, leak detection, and system flushing.
- Monitoring and Controls: Dashboard configuration and alarm management for real-time analytics.
Change Management
- Stakeholder Buy-In: Present TCO models and case studies to executives and facility teams.
- Vendor Partnerships: Establish clear SLAs and training programs with solution providers.
Future Research and Emerging Innovations
Beyond current practices, research is pushing liquid cooling into new frontiers.
Nanofluid Coolants
Engineered fluids with nanoparticles promise higher thermal conductivity and lower viscosity, enabling even greater heat flux removal.
Smart Cooling AI Agents
Machine learning models optimize coolant flow rates and pump speeds in real time, responding to workload fluctuations for peak efficiency.
Cryogenic and Supercritical Cooling
Experimental cryogenic loops using liquid nitrogen and supercritical CO₂ target quantum computing and next-gen AI clusters, where sub-zero cooling is required.
Liquid Cooling Myths Debunked
Clarifying common misconceptions to ease adoption concerns.
“Leaks Are Inevitable”
Modern fittings and sensors reduce leak risk to below 0.01% annually. Most incidents stem from poor maintenance, not technology flaws.
“Too Expensive for Most”
Early adopters saw 30% CAPEX premiums, but today’s modular systems and leasing options lower entry costs by 50% compared to five years ago.
“Only for Hyperscalers”
Liquid cooling scales from single-rack deployments to large data halls. Edge sites and SMBs increasingly embrace cold plates for targeted high-density applications.
Conclusion
Liquid Cooling in Data Centers is not just a cooling upgrade—it’s a transformational strategy for achieving peak performance, cost savings, and environmental stewardship. By understanding the technologies, market dynamics, TCO considerations, and operational best practices outlined here, you can lead your organization into a new era of efficient, reliable, and sustainable data center operations.
Ready to revolutionize your data center? Contact Reboot Monkey for a comprehensive Liquid Cooling in Data Centers assessment and begin your journey toward Cooler, Faster, Greener infrastructure.
Frequently Asked Questions
Q1: What is Liquid Cooling in Data Centers and why is it important?
Liquid Cooling in Data Centers uses coolant to directly remove heat from servers, offering superior efficiency and lower energy costs.
Q2: How does Liquid Cooling in Data Centers improve performance?
By maintaining stable operating temperatures, Liquid Cooling in Data Centers prevents thermal throttling and enables higher compute density.
Q3: Is Liquid Cooling in Data Centers suitable for existing facilities?
Many data halls can retrofit Cold Plate or Rear-Door solutions, making Liquid Cooling in Data Centers viable without full rebuilds.
Q4: Does Liquid Cooling in Data Centers reduce environmental impact?
Yes; Liquid Cooling in Data Centers cuts energy use by up to 60% and eliminates water loss in closed-loop configurations.
Q5: What are common challenges with Liquid Cooling in Data Centers?
Key concerns include CAPEX, leak mitigation, and staff training, but best practices and modular designs simplify adoption.
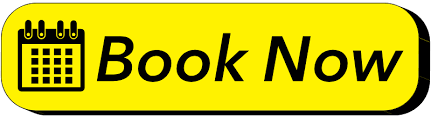